Exploring the Dimensions of Operational Excellence
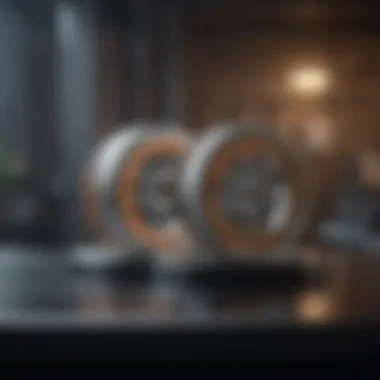
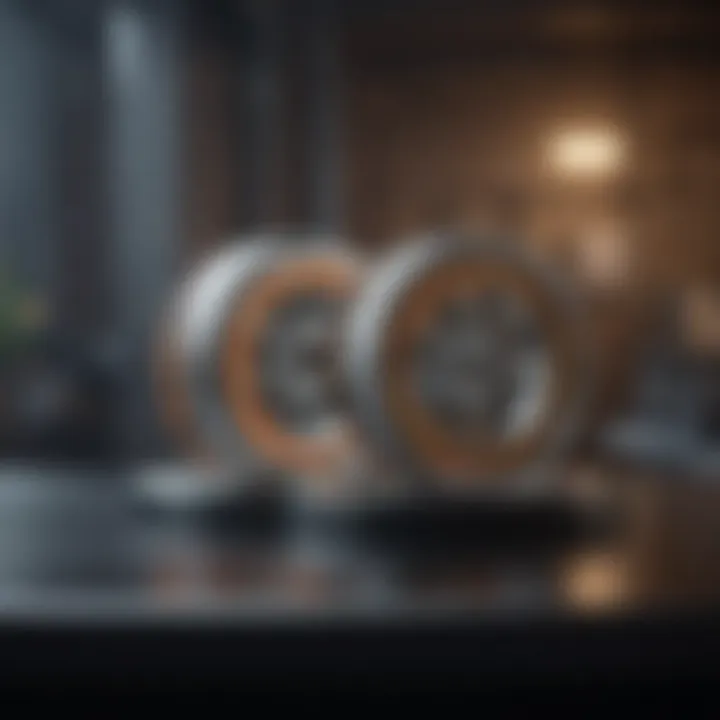
Intro
Operational excellence isnāt just a catchy phrase tossed into board meetings. It represents a fundamental shift in how organizations approach efficiency, productivity, and overall improvement. By adopting a mindset focused on achieving peak performance, businesses can not only streamline their processes but also create a sustainable environment for growth. The following sections will explore both the foundational concepts and advanced strategies associated with operational excellence, highlighting its relevance across various sectors.
Understanding Resilience, Well-Being, and Adaptability
Introduction to the concepts of resilience, well-being, and adaptability
In the fast-paced world of business, resilience, well-being, and adaptability act as the cornerstones of operational excellence. But what do these terms really mean? Resilience refers to the ability to bounce back from setbacks, whilst well-being encompasses both mental and physical health within an organization. Adaptability is the capacity to adjust effectively to changing circumstances.
Importance of these factors in personal and organizational development
When individuals and teams embody these traits, the benefits are far-reaching. For one, resilient employees are less likely to fall victim to burnout, maintaining higher levels of productivity even during difficult times. Furthermore, fostering well-being leads to improved morale and commitment among team members, which directly influences an organizationās culture. Adaptability serves as the glue that holds everything together, enabling teams to pivot and respond to market changes quickly. This interconnectedness plays a pivotal role in achieving true operational excellence.
Exploring strategies for cultivating resilience and well-being
How do organizations go about fostering these essential attributes? Here are several strategies to consider:
- Promote open communication: Encourage feedback and discussions to create an environment of trust.
- Implement wellness programs: Whether itās fitness allowances or mindfulness sessions, a focus on health shows commitment to well-being.
- Provide training and resources: Equip employees with tools that help them manage stress and build resilience.
- Celebrate adaptability: Recognize those who excel in adjusting to change, which cultivates a culture willing to embrace new challenges.
Identifying areas for improvement in these aspects can be invaluable. As organizations strive for excellence, acknowledging and cultivating resilience, well-being, and adaptability becomes a critical component of their journey.
"The ability to adapt to changing circumstances is not just a skill; itās a necessity in todayās business environment."
Principles of Operational Excellence
Defining operational excellence
At its core, operational excellence is about continuously improving an organizationās capabilities. It extends beyond mere efficiency; it factors in the value delivered to customers, employees, and other stakeholders.
Core principles
- Customer focus: Placing the customer at the center of āallā decision-making processes.
- Continuous improvement: A relentless pursuit to enhance processes, products, and services.
- Employee engagement: Meaningful involvement of employees at every level ensures that their insights drive improvements.
- Data-driven decision-making: Utilizing analytics to make informed choices rather than relying on gut feelings.
Methodologies Used to Achieve Operational Excellence
Various methodologies can be employed to guide organizations in their journey. Lean management, Six Sigma, and the Theory of Constraints are among the most prominent.
- Lean Management focuses on eliminating waste and improving workflow.
- Six Sigma concentrates on reducing defects in processes through data analysis.
- Theory of Constraints identifies the most significant limiting factors in processes and seeks to address them to improve overall system performance.
By understanding these methodologies, organizations can implement tailored strategies that resonate with their unique cultures and challenges.
Challenges and Opportunities
In their quest for operational excellence, organizations inevitably face hurdles. Resistance to change can stifle progress, while inadequate training may hinder the adoption of new processes. However, these challenges also present opportunities.
Embracing a growth mindset and actively learning from failures can carve pathways to breakthroughs.
Finale
As we unravel the threads of operational excellence, it becomes evident that this concept is about much more than operational metrics. It delves into the softer aspects, such as fostering a resilient and adaptable workforce. By internalizing these lessons and applying them in real-world contexts, organizations can not only stand the test of time but thrive in an ever-evolving landscape.
Understanding Operational Excellence
Operational excellence is more than just a buzzword tossed around in boardrooms; itās a crucial framework for organizations aiming to achieve sustainable growth and efficiency. This concept resonates deeply across various sectors, impacting everything from manufacturing to healthcare, and even service-oriented businesses.
Engaging with operational excellence entails more than ticking boxes on a checklist; it involves a thorough comprehension of the continuous cycle of process improvement, quality assurance, and customer satisfaction. The pursuit of this excellence fosters a culture that values agility, learning, and an unwavering commitment to meeting and exceeding expectations. Organizations that embrace these principles not only increase their operational effectiveness but also enhance their market competitiveness.
To truly grasp the significance of operational excellence, one must delve into its definitions and explore its historical evolution.
Defining Operational Excellence
At its core, operational excellence can be regarded as a management philosophy focused on improving an organization's overall performance. It stems from aligning processes and resources with customer needs and ensures the organization delivers value effectively.
Simply put, operational excellence is about doing things right the first time. This concept encourages organizations to minimize errors and waste while maximizing efficiency and productivity. Moreover, it emphasizes the importance of engaging employees at all levels. When employees are involved, they bring fresh perspectives that can unearth inefficiencies and drive systematic improvements.
To further illustrate this, consider a manufacturing company that adopts operational excellenceāthis company will continuously assess its supply chain processes, engage its workers in problem-solving, and leverage data-driven decision-making to enhance output.
The Historical Context
Understanding the historical backdrop of operational excellence is vital. Its roots can be traced back to various management philosophies such as Taylorism, Lean manufacturing, and Total Quality Management (TQM). Each of these frameworks contributed distinctive elements to the broader concept, shaping its evolution.
- Taylorism, developed by Frederick Winslow Taylor in the late 19th century, emphasized efficiency in mechanical processes through time motion studies.
- Lean manufacturing gained ground in the mid-20th century, particularly within the Toyota Production System, focusing on eliminating waste and creating value from the customer's perspective.
- Total Quality Management (TQM) emerged as a comprehensive approach in the 1980s and 1990s, prioritizing quality at every level of the organization, encouraging a culture of constant improvement.
In todayās fast-paced business landscape, organizations must look back at these philosophies while also adapting to the digital age. The interplay of historical practices and contemporary technologies has set the stage for modern operational excellence strategies. Understanding past developments in this domain allows for a more nuanced approach to current and future operational challenges.
"True operational excellence emerges from the marriage of historical insights and modern innovation, creating a dynamic and responsive organization."
By gleaning lessons from history and systematically implementing robust operational approaches, organizations can craft unique strategies to tackle challenges and leverage opportunities in their pursuit of excellence.
Core Principles of Operational Excellence
Operational excellence is not merely an aspiration; it's a framework of principles that guide organizations toward achieving extraordinary performance and improved outcomes. These principles serve as a solid foundation for any organization aiming to enhance its operations, ensuring not only survival but sustained growth in today's fiercely competitive landscape. Understanding these core principles helps businesses to align their resources, strategies, and culture in a manner that promotes efficiency, effectiveness, and continuous progress.
Customer Focus
At the heart of operational excellence lies a resolute focus on the customer. Businesses must recognize that without their customers, their operations are akin to a ship without a sail. Cultivating this focus means understanding customer needs, expectations, and experiences.
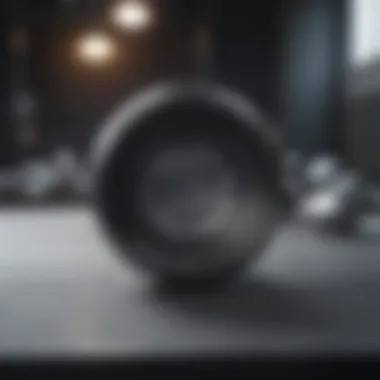
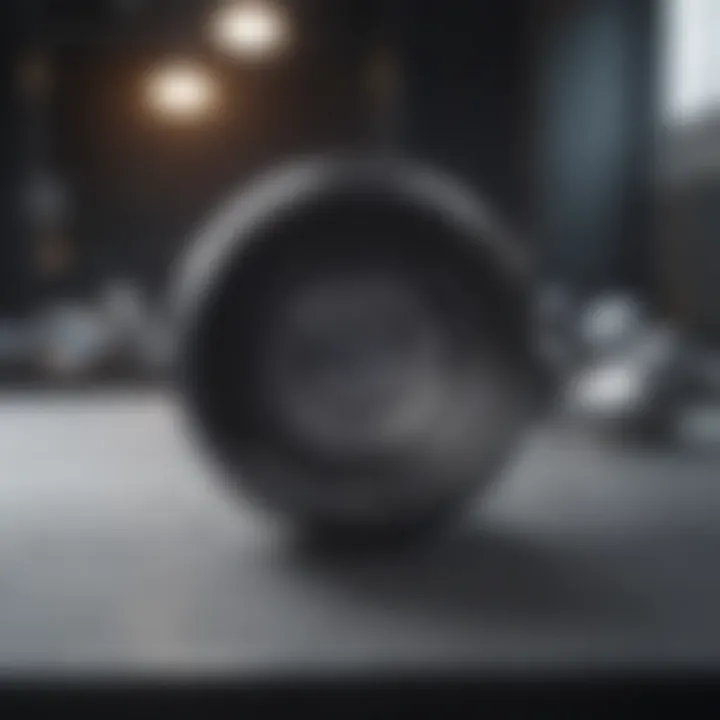
- Building relationships: Engaging with customers is crucial. This can be done through feedback mechanisms, surveys, and direct interactions, which can provide invaluable insights.
- Personalizing experiences: Tailoring products and services to meet specific customer preferences leads to increased satisfaction. Companies like Amazon exemplify this approach by using sophisticated algorithms to recommend products based on individual user behavior.
- Responsive service: Rapidly addressing customer concerns shows that a business values its clientele. A proactive approach, like those implemented by Zappos, builds a customer-centric reputation.
The benefits of a customer-focused strategy are considerable. Higher customer satisfaction not only improves loyalty but also cultivates a positive word-of-mouth, which can be a game changer in gaining new clients.
Continuous Improvement
Continuous improvement is a mindset, a culture within an organization that fosters ongoing efforts to enhance products, services, or processes. It doesnāt settle for mediocrity. Instead, it strives to evolve and adapt. This principle is commonly realized through methodologies like Lean and Six Sigma.
- Kaizen philosophy: Embracing small, incremental changes can lead to substantial improvement over time. Employees at every level should feel empowered to suggest improvements; fostering such an environment can spark significant advancements.
- Data-driven decisions: Collecting and analyzing data helps identify areas needing improvement, making it easier to implement corrective action based on solid evidence rather than guesswork.
- Feedback loops: Establishing communication channels for feedback leads to continual refinement. For example, Toyota incorporates regular feedback sessions to ensure that processes and workflows are continually optimized.
Organizations that prioritize continuous improvement often benefit from increased efficiencies, reduced waste, and greater profitability.
Employee Engagement
No operational excellence model can succeed without the crucial element of employee engagement. Employees are the lifeblood of any organization. When they feel involved, appreciated, and invested in their work, their productivity can soar.
- Empowerment: Allowing employees to take ownership of their roles encourages a sense of responsibility. When people feel that their efforts impact the organization, they tend to perform at higher levels.
- Training and development: Providing opportunities for professional growth not only equips employees with the skills they need but also conveys that the organization cares about their future. Companies investing in employee development often enjoy lower turnover rates and higher job satisfaction.
- Recognition: Acknowledging employee contributions fosters a better working atmosphere. Simple gestures, like shout-outs in meetings or an employee of the month program, can go a long way in promoting morale.
Ultimately, when employees are engaged, they are more likely to contribute meaningfully to the organization's goals, resulting in improved outcomes both for the organization and its workers.
āOperational excellence is a journey, not a destination. It requires constant attention, adaptation, and commitment from everyone, from top management to front-line employees.ā
In sum, the principles of customer focus, continuous improvement, and employee engagement create a robust framework for operational excellence. They not only drive efficiency and effectiveness but also instill a culture of adaptability and resilience, vital for thriving in the ever-evolving marketplace.
Operational Excellence Frameworks
Operational excellence is not just a buzzword tossed around in boardrooms; it's a proven approach that transforms how organizations work. The frameworks that support operational excellence are crucial because they provide structured methods to drive efficiency, quality, and team morale. Understanding these frameworks is paramount for anyone keen on fostering a culture of continuous improvement in their workplace.
Lean Methodology
Lean methodology emphasizes minimizing waste while maximizing value. This approach isnāt about cutting costs blindly; instead, it encourages a thorough examination of the processes involved in delivering products or services. By removing unnecessary steps, organizations can streamline operations, leading to faster delivery times and enhanced customer satisfaction.
A few key principles of Lean include:
- Value Stream Mapping: Identifying all actions (value-adding and non-value-adding) in a process.
- Just-In-Time Production: Only producing what is needed, when it is needed.
- Kaizen: Continuous improvement efforts by all employees, not just management.
Adopting Lean practices can directly enhance profitability by lowering operational costs and increasing speed. The beauty of Lean is seen in manufacturing giants like Toyota, which have applied these principles effectively to lead in the automotive industry.
Six Sigma
Six Sigma offers a discipline that uses data and statistical analysis to improve and sustain the quality of processes by identifying and removing defects. Originally developed by Motorola in the 1980s, Six Sigma focuses on reducing variation and ensuring that processes operate at their maximum efficiency.
It is based on a few core concepts:
- DMAIC (Define, Measure, Analyze, Improve, Control): A structured problem-solving methodology for improving existing processes.
- DMADV (Define, Measure, Analyze, Design, Verify): Used for creating new processes or products at Six Sigma quality levels.
Firms like General Electric have embraced Six Sigma and reaped substantial benefits, resulting in massive cost savings and improvements in quality. By focusing on measurable outcomes, Six Sigma not only enhances operational efficiency but significantly reduces errors, thus raising customer satisfaction.
Agile Practices
Agile practices, stemming from software development, prioritize flexibility and rapid response to change. The beauty of Agile lies in its iterative approach, allowing teams to adapt quickly to feedback and changing requirements. Itās about putting the customer at the center and embracing uncertainty.
For teams looking to implement Agile, a few practices can be beneficial:
- Scrum: A framework for managing complex projects, allowing teams to work in small, cross-functional groups.
- Kanban: A visual method to manage work as it moves through a process, focusing on efficiency and flow.
Many organizations, especially tech startups, have found that Agile practices not only foster team collaboration but also lead to quicker product releases and higher customer satisfaction. Companies like Spotify have showcased the efficiency of Agile, adapting it to suit their unique needs, thus standing as a testament to its effectiveness.
"The root of operational excellence lies in a strong framework; without it, organizations may drift and lose their way in the complex waters of market demands and competition."
In summary, these frameworksāLean, Six Sigma, and Agileāare not just methodologies; they form the backbone of a systematic approach to operational excellence. Each framework brings its unique strengths, offering tailored solutions to different organizational challenges. Embracing these frameworks is the first step toward moving from theory to practice, ensuring that operational excellence is not merely a goal but a reality.
Implementing Operational Excellence
Implementing operational excellence is like planting a seed; it requires careful consideration, planning, and consistent nurturing to truly flourish. Organizations striving for operational excellence need to be more than just aware of it; they must actively integrate its principles into their daily practices. This section delves into how businesses can lay the groundwork for excellence through strategic planning, cultural transformation, and ongoing training and development.
Strategic Planning
Strategic planning serves as the backbone of operational excellence. A well-crafted plan helps organizations navigate the often-turbulent waters of change and align resources effectively to meet desired outcomes. When it comes to operational excellence, a strategic plan should emphasize the long-term vision while maintaining flexibility for adjustments along the way.
To kickstart this process, organizations should consider key components such as:
- Setting Clear Objectives: Outline specific, measurable, achievable, relevant, and time-bound (SMART) goals. This clarity helps teams stay focused and measure progress accurately.
- Identifying Key Metrics: Establish performance indicators that will track the effectiveness of operational changes. This can include efficiency ratios, customer satisfaction scores, and turnover rates.
An important part of this strategic planning is involving all layers of the organization. Decision-makers need insights from frontline employees who understand operational nuances. Through this collaborative approach, companies ensure that their operational strategies reflect real-world conditions, creating a more robust framework for excellence.
Cultural Transformation
Cultural transformation is pivotal in embracing operational excellence. It's not enough to introduce new processes; organizations must reshape their culture to support a mindset of continuous improvement. Culture is the invisible glue that holds everything together. A positive workplace culture fosters creativity and ownership among employees, encouraging them to contribute ideas for enhancements.

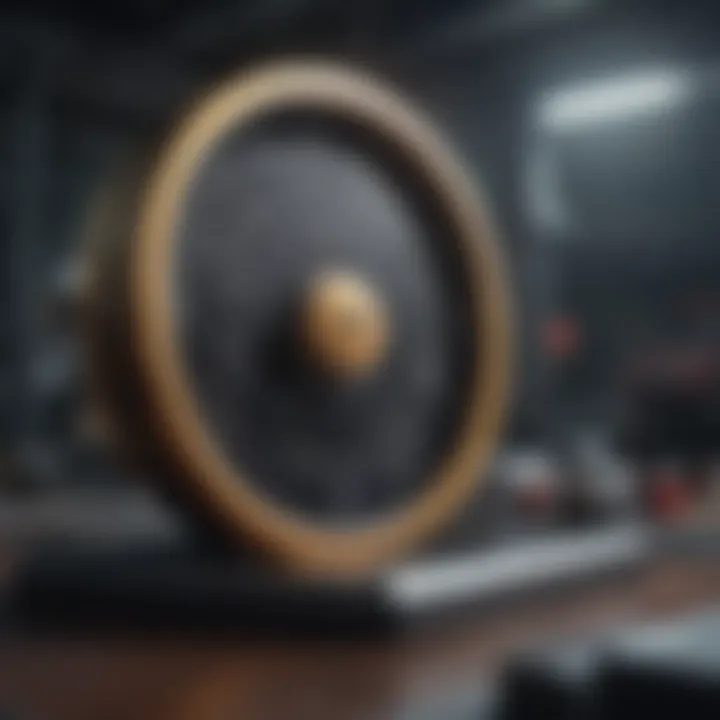
Considerations for nurturing a culture ripe for operational excellence include:
- Encouraging Open Communication: Leadership should create channels for feedback, where employees feel safe to voice concerns and suggest improvements.
- Celebrating Small Wins: Acknowledge accomplishments, no matter how minor they may seem. Celebrating successes reinforces positive behavior and motivates the team.
"A culture focused on operational excellence is not just about processes; it's about the people behind them."
Training and Development
Training and development are essential components that keep the momentum of operational excellence alive. Regular training equips employees with the skills they need to adapt to changing environments and methodologies. Organizations need to ensure they arenāt just training people for the sake of it, but are genuinely upskilling them to be better contributors.
Effective training programs should address:
- Tailored Training Sessions: Customized programs that speak to specific roles within the company can foster deeper understanding and relevance.
- Continuous Learning Opportunities: Encourage a culture of lifelong learningākeeping skills fresh will help teams meet challenges head-on and stay ahead in the game.
By thoughtfully integrating these elements into their operations, organizations can build a framework that not only achieves operational excellence but sustains it over the long haul. Adopting these principles allows for an environment that is adaptive, responsive, and ultimately successful.
Challenges in Achieving Operational Excellence
Operational excellence isnāt a walk in the park. It demands a clear grasp of various hurdles that string together across industries and enterprises. The quest for operational excellence is not just about adopting methods but also about overcoming significant barriers that can stall progress and hinder effectiveness. Understanding the challengesāespecially those related to resistance to change, resource constraints, and misalignment of goalsānot only prepares organizations for inevitable bumps in the road but also creates pathways for finding solutions that can lead to a sustainable operational framework.
Resistance to Change
One of the biggest obstacles in the pursuit of operational excellence is simply the resistance to change. It's a common human tendency to cling to familiar processes and avoid those that require an overhaul of established routines. Operational excellence, by its own nature, often necessitates profound changesāa real shake-up of existing practices, whether one's talking about workflow, team dynamics, or technology usage.
Implementing operational excellence means pushing employees out of their comfort zones. People might feel threatened by alterations in job descriptions, or fear they may become obsolete. To mitigate this resistance, leaders need to cultivate a culture that emphasizes open communication and transparent change management. When employees feel involved in discussions about upcoming changes, they are more likely to embrace a transformational mindset. Some steps to consider are:
- Educating Staff: Training programs that explain the benefits and necessity of operational excellence can ease fears.
- Involvement in Decision-Making: Including team members in the decision-making process fosters a sense of ownership and control.
"Change is hard at first, messy in the middle, and gorgeous at the end."
Resource Constraints
Sometimes the gears that drive operational excellence are stalled due to finite resources. Cost, time, and human capital can all be limiting factors in realizing operational goals. Not every organization has endless resources availableāespecially smaller businesses or those facing economic challenges. Budget cuts might trim the ability to invest in new technologies or training.
Resource constraints also lead to prioritization issues. Companies might be forced to choose which operational areas to enhance first, leaving vital aspects behind. Strategic allocation of resources is critical here. Complexities arise when collaboration among departments is needed, making it essential to find a balanced approach to resource management.
To work around this, organizations can:
- Identify Core Priorities: Focus on key operational areas that align with long-term objectives.
- Utilize Technology: Leveraging existing technology to optimize workflows can compensate for limited resources.
Misalignment of Goals
Another formidable challenge is the misalignment of goals. In many organizations, departments often operate in silos with different objectives and outcomes. When the vision for operational excellence isn't uniformly understood or agreed upon, the outcomes can be chaotic.
For example, if the marketing department is aiming for swift customer engagement while the production side is focused on reducing costs, then both may encounter issues that lead to conflict. The success of operational excellence won't resonate uniformly across the organization if various teams are pulling in different directions.
Achieving alignment requires:
- Setting Unified Goals: Clearly articulated and measurable targets should be communicated across all levels.
- Regular Check-ins: Periodic reviews can help ensure that all departments remain aligned and track progress together.
Benefits of Operational Excellence
Operational excellence is not just a fancy term bandied about in boardrooms; it is a critical framework that can dramatically enhance an organization's performance. Embracing operational excellence leads to a myriad of benefits that directly and indirectly impact every facet of an organization. This section will unpack the most significant benefits, delving into aspects such as enhanced efficiency, improved quality, and greater employee satisfaction.
Enhanced Efficiency
When an organization seeks operational excellence, it often sees a remarkable uptick in efficiency across its processes. Utilize Leans principles, for instance, which streamline workflows by reducing waste. This means that time, financial resources, and human efforts are allocated more effectively, resulting in a more agile organization.
Employees can focus on high-value tasks instead of getting mired in bureaucratic red tape. Strategies like process mapping or kanban systems serve to eliminate bottlenecks that might previously have slowed down production or service delivery. For example, Toyota's production system exemplifies enhanced efficiency; they managed to reduce inventory costs while maximizing output.
- Key strategies to enhance efficiency:
- Lean methodologies
- Process automation
- Continuous feedback mechanisms
Implementing these practices not only improves output but also enables an organization to quickly adapt to changes in market demand. In today's fast-paced environment, agility is not just an advantageāit's a necessity. Organizations aiming for operational excellence are better positioned to pivot when disruptions arise, leading to sustained competitive advantage.
Improved Quality
Quality management emerges as another cornerstone of operational excellence. Organizations that are committed to excellence integrate quality assurance into every phase of their operations. This ensures that the product or service meets established standards consistently, ultimately leading to a reduced defect rate.
Utilizing Six Sigma practices is one effective way to boost quality control. By identifying and removing the causes of defects, organizations not only enhance customer satisfaction but also foster brand loyalty. Companies like General Electric have seen remarkable improvements in their processes by systematically focusing on quality.
- Benefits of improved quality:
- Increased customer trust
- Reduced costs related to defects
- Enhanced market reputation
Moreover, a focus on quality can lead to innovations in products or services. Engaging employees in quality improvement initiatives often unleashes their creativity. It becomes a win-win situation; customers receive superior products, and organizations see an uptick in profitability.
Greater Employee Satisfaction
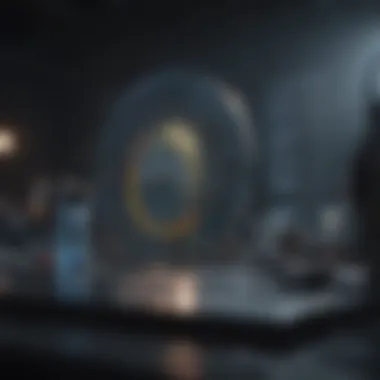
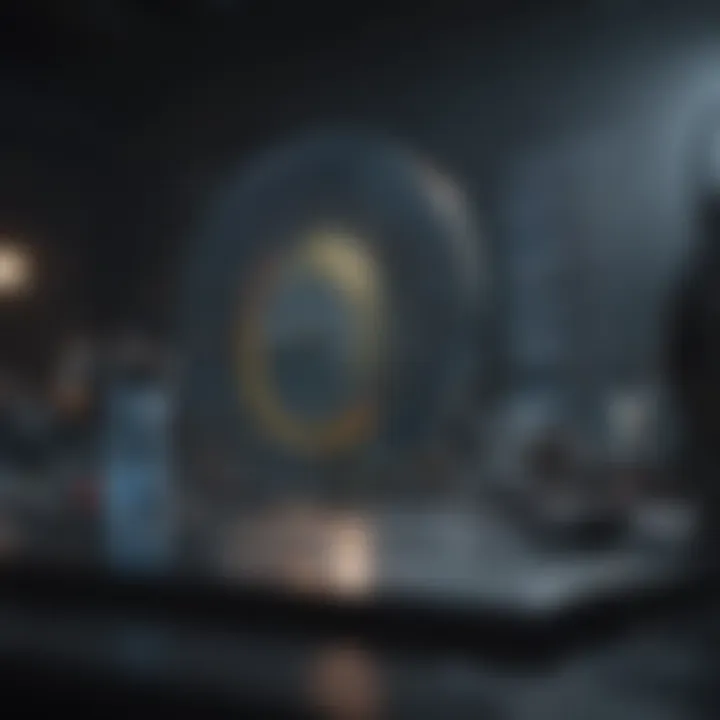
Last but definitely not least, operational excellence plays a crucial role in fostering a satisfied workforce. An organization that prioritizes excellence tends to value transparency, employee input, and career growth. When employees see their contributions as meaningful, it bolsters their morale significantly.
Imagine a workplace where every team member feels empowered to voice their ideas. Leading organizations often adopt systems that recognize employee contributions, which not only enhances job satisfaction but also encourages continuous engagement. Google, for example, is renowned for its culture of encouragement and innovation, resulting in exceptionally high employee satisfaction rates.
- Aspects related to employee satisfaction:
- Inclusive decision-making
- Opportunities for skill development
- Recognition programs
As the landscape of business continues to evolve, those committed to operational excellence will find themselves ahead of the curve, effectively navigating any storm ahead.
Measuring Operational Excellence
Measuring operational excellence is a pivotal endeavor for organizations aiming to enhance their performance and sustain competitive advantages. It's not merely about having a vague idea of what's working and what isn't, but taking a structured approach to evaluate and refine business processes. When businesses measure operational excellence effectively, they are better positioned to identify successes and pinpoint areas needing improvement. The framework of assessment allows organizations to align their strategies with actual outcomes, streamlining efforts and maximizing resources.
Key Performance Indicators
Key performance indicators (KPIs) serve as the compass guiding organizations on the path to operational excellence. These metrics provide objective data that reflects the health and efficiency of business operations. Here are some essential KPIs organizations should consider:
- Customer Satisfaction Scores: Measures how products or services meet or exceed customer expectations.
- Cycle Time: Indicates the time taken from the start to the completion of a process. Shorter cycle times often align with higher efficiency levels.
- Error Rates: Looks at the frequency of mistakes in processes, helping to identify areas for improvement.
- Employee Turnover Rates: A healthy organization is often reflected by lower turnover rates, indicating employee satisfaction and engagement.
Implementing effective KPIs involves a few fundamental steps:
- Define Clear Goals: Understanding what success looks like helps in selecting the appropriate KPIs.
- Collect Data Routinely: Data should be gathered consistently to identify trends over time.
- Analyze and Adjust: Examination of the data allows for adjustments in strategies to better meet organizational goals.
"What gets measured gets managed." ā Peter Drucker
Benchmarking Practices
Benchmarking is a critical practice that complements the measurement of operational excellence. It's the process of comparing business processes and performance metrics to best practices from other organizations. By studying these benchmarks, companies can identify gaps in their operations and strive for improvement. There are various types of benchmarking:
- Internal Benchmarking: Involves comparing practices within different departments in the same organization.
- Competitive Benchmarking: Focuses on comparing performance with key competitors in the market.
- Functional Benchmarking: Looks at similar processes in different industries to draw insights.
Engaging in benchmarking has several advantages:
- Informs Strategy Development: Provides insights into successful practices that can be adapted.
- Fosters Innovation: Exposure to best practices encourages creative solutions to operational challenges.
- Encourages Accountability: It builds a culture of continuous improvement as organizations strive to meet or exceed benchmarks.
Case Studies
Understanding how operational excellence comes to life requires a look at real-world examples, and thatās where case studies shine. They shed light on the practical applications and implications of the principles discussed earlier. Each case study serves as a slice of reality, illustrating the ups and downs of implementing operational excellence strategies. This not only offers insight into the immediate impacts but also helps to navigate the long-term journey toward sustaining excellence.
Industry Leaders
When examining industry leaders, it becomes clear that operational excellence isn't just a nice-to-have; it's often a necessity in highly competitive markets. Take Toyota, for instance. Their commitment to the Lean methodology has allowed them to become a symbol of efficiency. The Toyota Production System emphasizes minimizing waste while maximizing value.
Key components of their approach include:
- Just-in-Time Production: This minimizes inventory costs and reduces waste by producing only what is needed at any given time.
- Continuous Improvement (Kaizen): Employees at all levels are encouraged to regularly suggest and implement improvements. It plays a crucial role in fostering a culture of innovation.
- Quality Control: Inspecting materials and processes continuously reduces defects.
By focusing on these elements, Toyota not only enhances productivity but also elevates customer satisfaction. Their example reveals that when operational excellence is embedded in a company's culture, success follows like a shadow.
Small and Medium Enterprises
Small and medium enterprises (SMEs) often find operational excellence to be a double-edged sword. On one hand, they may lack the resources of larger corporations; on the other, they can be incredibly agile and able to implement changes quickly.
For example, a local bakery might adopt Lean practices by analyzing its workflow. By reorganizing the kitchen layout to reduce unnecessary movement and waste, the bakery increases its baking output while ensuring fresh, quality products. This not only lowers costs but also meets customer demands without compromising quality.
Critical elements for SMEs to consider when pursuing operational excellence include:
- Resource Management: Effective allocation of limited resources can yield significant benefits.
- Employee Empowerment: Engaging employees in decision-making can cultivate a sense of ownership and drive efficiency.
- Feedback Loops: Regularly collecting and acting on customer feedback helps align services and products with market demand.
āThe only way to do great work is to love what you do.ā ā Steve Jobs
This quote resonates particularly well with SMEs, where passion and dedication can lead to remarkable results in quality and efficiency.
In summation, not only does the practice of examining these case studies help illuminate best practices, but it also serves to inspire organizations, big and small, to embrace operational excellence as a pathway to sustainable success. Viewing operational excellence through the lens of real-world examples equips professionals with actionable insights and lessons learned from the field.
Future Trends in Operational Excellence
The landscape of operational excellence is ever-evolving, pushing organizations to rethink their strategies and adapt to new realities. As the global market shifts and technological advancements emerge, understanding the future trends in operational excellence becomes crucial. This section will delve into technology integration and sustainability practices, both pivotal in shaping how organizations operate in the coming years.
Technology Integration
In an era where digital transformation reigns supreme, technology integration is not just a trend; itās a necessity. Organizations are increasingly leveraging cutting-edge tools and platforms to streamline processes, enhance productivity, and improve decision-making. The infusion of technology into operational excellence can lead to significant benefits:
- Automation of Processes: Robotic Process Automation (RPA) is making waves by reducing manual tasks, allowing employees to focus on strategic, high-value activities.
- Data Analytics: Businesses are utilizing big data to gain insights that drive continuous improvement. Data not only guides operations but also personalizes customer experiences,
- Real-time Monitoring: IoT devices facilitate real-time performance monitoring, enabling quick adjustments and fostering agile practices.
Implementing these technologies means investing wisely. Itās about finding the right balance and making the technology work for your organizational goals.
"Technology, when leveraged correctly, can be the cornerstone of operational excellence.''
Sustainability Practices
As we pivot to sustainability practices, we see that they are becoming increasingly intertwined with the concept of operational excellence. Companies are recognizing that sustainability is not merely a compliance issue or an ethical consideration; itās a vital component of long-term success. Key elements include:
- Resource Efficiency: Streamlining processes to utilize resources more effectively can result not only in cost savings but also in a reduced environmental footprint.
- Corporate Social Responsibility (CSR): Thereās an expectation from consumers for companies to act responsibly. Integrating sustainable practices into operations can enhance brand reputation and customer loyalty.
- Innovation and Adaptability: Organizations that embrace sustainability often lead in innovation, adapting quickly to market changes and consumer preferences.
By embedding sustainability into the operational framework, firms can create a competitive edge. Eventually, this leads to a cycle where sustainable practices drive efficiency, which in turn fosters further sustainability initiatives. Understanding this symbiotic relationship is key for future-focused organizations.